Chains and Their Types
- Share
- Issue Time
- Apr 11,2022
Summary
A chain is a series of connected links, usually made of metal. A chain may consist of two or more links. Chains can be classified in many different ways, and there are also many different types.
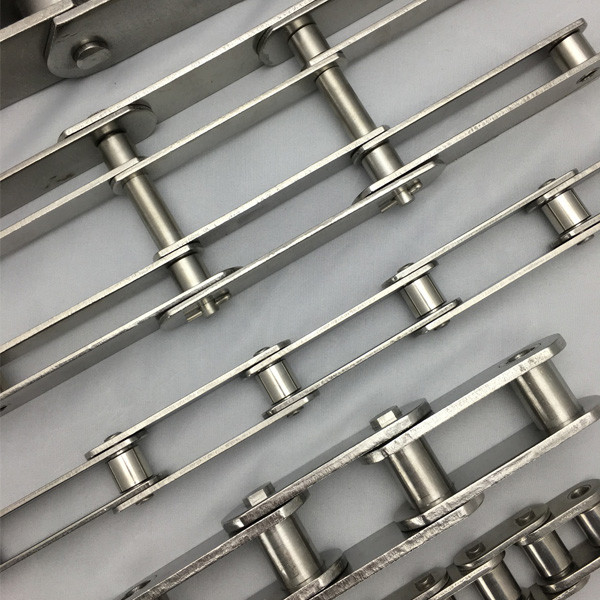
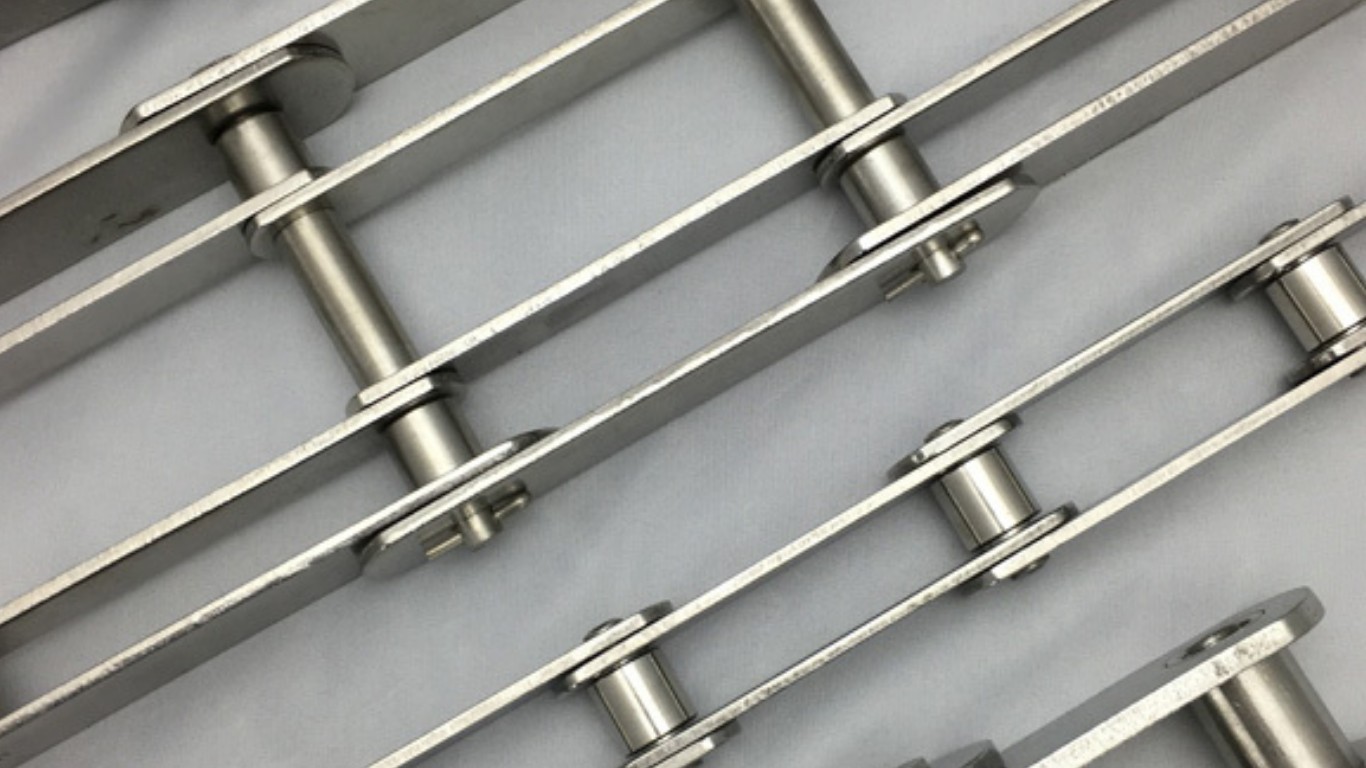
A chain is a series of connected links, usually made of metal. A chain may consist of two or more links. Chains can be classified in many different ways. In theory, a chain is a continuous flexible rack that meshes with teeth on a pair of gears. A sprocket is a gear whose teeth are shaped to mesh with a chain, a form of gear. From a historical and developmental perspective, a chain is a mechanical belt that runs on sprockets and can be used to transmit power or convey materials.
Chain types
From an industry point of view, the main types of chains are roller chains, leaf chains, silent chains, engineering chains, and flat-top chains. This article mainly introduces roller chains and engineering chains.
The main purpose of the rollers is to reduce friction, but the rollers in the chain have two separate functions, usually provided by the same roller.
The diameter of the rollers in a drive chain is usually smaller than the height of the chainplates. Thus, the chainplate acts as a guide when the chain is engaged with the sprockets, and can also do the same when the chain rides on the guide, such as in a bucket elevator.
The rollers on a conveyor chain usually have a diameter much larger than the width of their adjacent sidebars. This is done for two reasons, (i) large rollers called load rollers carry the sidebars above the conveyor track, preventing friction, and (ii) larger rollers have some rotational friction relative to smaller rollers mechanical advantage, thereby helping to reduce chain tension.
The idlers in most chains are also used to mesh the sprockets. However, load-bearing rollers equipped with antifriction bearings are sometimes used as outboard rollers on rollerless chains. Rollerless chains are similar in appearance to chains with rollers and are used in applications that do not require rollers.
There are many types of roller chains, each designed for a specific purpose. All roller chains are constructed so that the rollers are evenly distributed throughout the chain. A major advantage of roller chains is that the rollers rotate when they contact the sprocket teeth.
Two types of roller chains are commonly used, (i) single-strand and (ii) multi-strand. In a multi-strand, two or more chains are assembled side-by-side on common pins that maintain the alignment of the rollers in the multi-strand.
Standard roller chains are defined as pitch proportional, which makes them different from other types of roller chains. The nominal size of these chains is roughly proportional to the chain pitch, which is the distance between the centers of adjacent joint components.
The three most important roller chain dimensions are pitch, roller diameter, and inner chain width. These dimensions determine the fit between the chain and sprocket. Roller chains are used in drive and transmission applications. Each application area has a series of independent chains.
Engineering class chains were first developed in the 1880s. They were developed for increased strength, speed, and impact resistance, as well as better dimensional control. Early engineered chains were designed for difficult conveying applications.
Like roller chains, engineered chains are developed as all-steel products made from rolled shapes. One exception is that the rollers, especially flanged rollers, are made of cast iron, and this exception continues to this day.
Larger size engineering class chains were quickly developed. Increased spacing, strength, wear life, and load-carrying capacity to meet the heavy-duty demands of the industry. Engineered class chains are developed to operate reliably under the most demanding conditions.
Many different types of engineering class chains are used for various applications. Most engineered chains are used on conveyors, bucket elevators, and tension links. Only a few are used for drives. The main design considerations for these chains are tensile loads, several types of wear, lubrication, and the environment. Key design considerations for engineered chains for drives include various tensile loads, certain types of wear, roller and bushing impact, and wear.
The size of the engineering conveyor chain is not proportional to the pitch. The clearances between the moving parts of engineered chains are usually much larger than for roller chains of the same size. The clearances between pins and bushings, bushings and rollers, and inner and outer links are proportionally much larger. Larger clearance is provided so that dust and debris can escape freely from the bearing area. Therefore, debris is less likely to clog the joints of the chain, causing them to stick or get stuck.
Engineered chains in conveyors or drives may be exposed to all tensile loads. However, tensile loads from centrifugal force, chord action, and vibration are unlikely to be major factors. Therefore, engineering chains must have certain tensile strength properties to withstand the wide range of tensile loads that may be imposed on them.
Wear is probably the most important parameter when designing engineered steel chains. Joint wear, roller and bushing wear, and sidebar and track wear are all very important conveyor chain concerns. Joint wear and roller and sprocket wear are major problems with drive chains.
When the chain runs on the sprocket, the joints are articulated and material wears from the outer diameter of the pin and the inner diameter of the bushing, and as this material wears away, the chain gets longer.
Engineered chain sprockets are designed to withstand 3% to 6% wear elongation. When the chain stretches past that point, it no longer fits the sprocket and the system doesn't function properly.
Roller wear in drive chains is usually not a major problem, but roller wear in conveyor chains can be a serious problem. Worn teeth on the small sprocket can put a large shock load on the chain. Roller and bushing wear, as well as side rod and track wear, are very important considerations in the design of engineered steel roller conveyor chains.
Lubrication is a major concern in designing engineered steel conveyor chains. Many engineered conveyor chains must operate with little or no lubrication, so the material selection is very important.
The environment is a major concern when designing engineered conveyor chains. Standard conveyor chains should work under mildly corrosive conditions. Some conveyor chains also operate in highly abrasive conditions. High wear conditions are commonly found in mining and material handling. Extreme temperatures are usually not a major concern when designing standard engineering class chains.
There are many general types of engineering class chains. Those with steel rollers are probably the most widely used on drives and conveyors. Bushed rollerless versions meet the needs of many conveyor and bucket elevator applications.
The above describes the types and uses of roller chains and engineered chains. If you are planning to buy chains for you or your factory, please contact us.
As a quality custom chain and component supplier, our products are Roller Chains, Forged Chains, Conveyor Chains, Welded Steel Chains, Closed Track Chains, Sprockets, Components, etc. State-of-the-art machinery in machining, stamping and stamping, heat treatment, welding, and chain assembly, dedicated to high-quality standards. We provide dedicated testing, on-site inspections, coordination, and detailed documentation to ensure a quality product every time.